Understanding Plastic Injection Mold Tooling Service
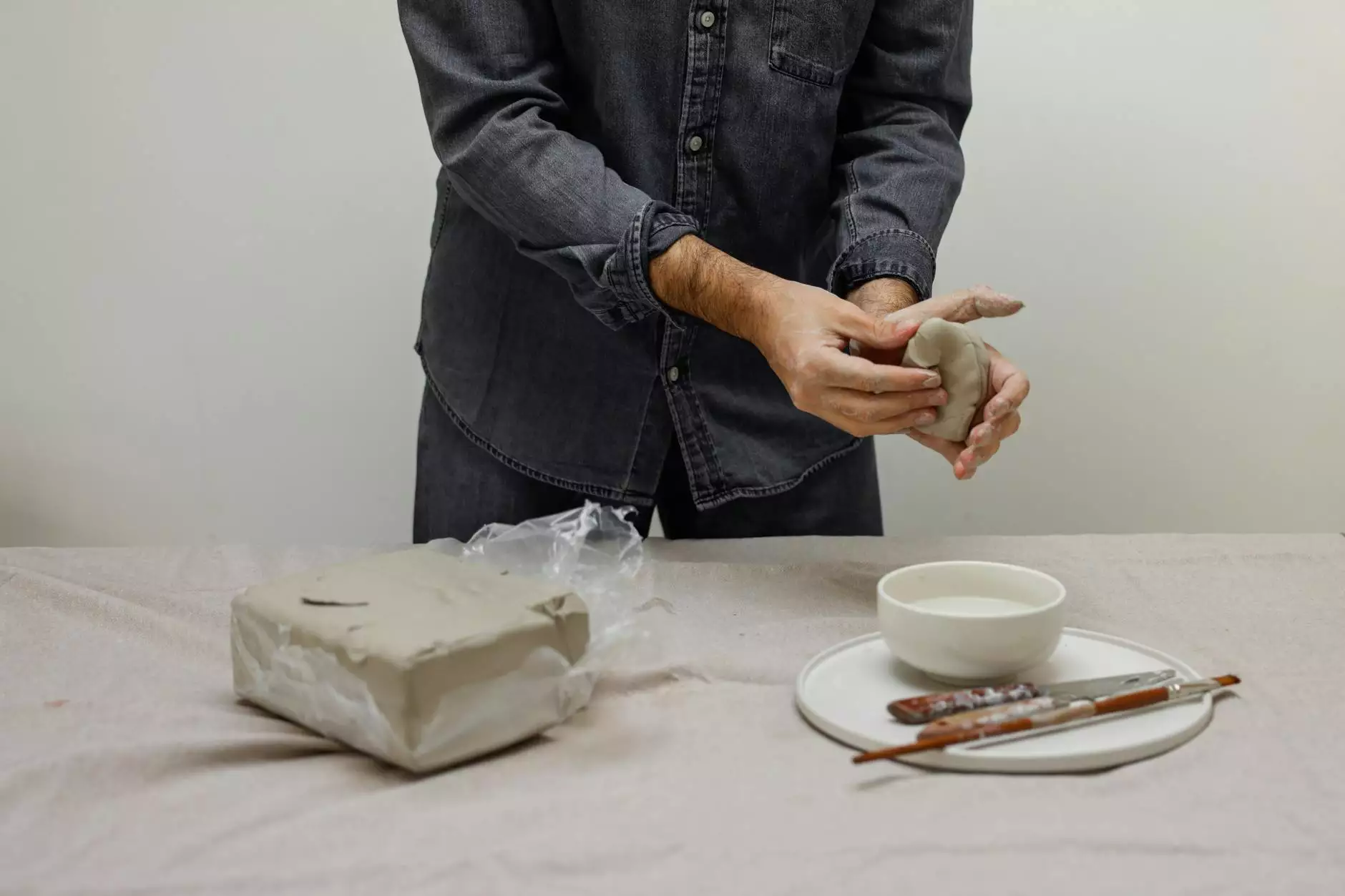
Plastic injection mold tooling service is a vital aspect of modern manufacturing, offering precision, efficiency, and versatility in producing a wide array of plastic components. As industries increasingly rely on plastic products, understanding the nuances of this service becomes essential for businesses aiming to optimize their production processes.
What is Plastic Injection Mold Tooling?
Plastic injection mold tooling involves the creation of molds that are used to shape molten plastic into desired forms and designs. This manufacturing process is characterized by injecting heated plastic materials into a mold under high pressure, allowing for the rapid production of complex parts with high precision.
Benefits of Plastic Injection Mold Tooling
The benefits of utilizing a plastic injection mold tooling service are numerous and impactful, particularly for companies focused on efficiency and quality:
- High Precision: Injection molding can produce parts with tight tolerances and intricate designs.
- Cost-Effectiveness: Mass production using injection molds significantly reduces costs per unit as the process scales.
- Speed: The speed of production is unparalleled, with cycle times typically ranging from a few seconds to a few minutes.
- Material Versatility: A variety of thermoplastics and thermosetting plastics can be used, allowing for material flexibility based on project needs.
- Consistency and Quality: Once the mold is created, each part produced is almost identical, ensuring consistent quality across large production runs.
The Process of Plastic Injection Mold Tooling
The process behind plastic injection mold tooling service can be broken down into several key steps, each of which plays a critical role in the overall outcome:
- Design: The initial phase involves creating a mold design that accurately reflects the desired part specifications. CAD software is often used for precision.
- Material Selection: Depending on the desired properties of the final product, various materials can be chosen, such as ABS, PVC, or polypropylene.
- Mold Fabrication: Using CNC machining, the mold is fabricated with extreme precision. This step is crucial, as any imperfections can lead to defects in the final product.
- Testing: After the mold is created, it undergoes rigorous testing to ensure it meets quality standards and performs as expected with the chosen materials.
- Production: Once testing is complete, the mold can be used for mass production. Molding machines inject the heated plastic into the mold, cooling and solidifying the part.
Applications of Plastic Injection Mold Tooling
The applications of plastic injection mold tooling services span a vast range of industries. Some notable applications include:
- Aerospace: Lightweight and durable plastic parts for aircraft components.
- Automotive: Custom plastic parts used in car interiors, exteriors, and critical engine components.
- Consumer Electronics: Housing for devices such as smartphones and tablets, with complex designs that fit ergonomic needs.
- Medical Devices: Precision components that meet strict regulatory standards for safety and efficacy.
- Packaging: Bottles, containers, and other packaging solutions designed for functional use and aesthetic appeal.
Quality Control in Plastic Injection Mold Tooling
Quality control is a critical component of plastic injection mold tooling service. The following techniques ensure the highest standards are met:
- First Article Inspection: Thorough inspection of the first few produced parts to establish baseline quality.
- Statistical Process Control (SPC): Monitoring production processes using statistical methods to identify and mitigate variations in quality.
- Regular Maintenance: Ensuring molding machines and tools are regularly maintained to prevent defects caused by equipment failure.
- Feedback Loops: Implementing feedback mechanisms from production to design teams to continuously improve the mold design and production processes.
Choosing the Right Plastic Injection Mold Tooling Service Provider
When selecting a plastic injection mold tooling service provider, consider the following factors to ensure that your project is in capable hands:
- Experience: Look for a provider with a proven track record in your specific industry or application.
- Technical Expertise: Ensure they have advanced technical capabilities and access to the latest technologies and techniques in mold making.
- Customer Reviews: Check testimonials and case studies from past clients to gauge satisfaction and trustworthiness.
- Support Services: Consider whether they offer additional services such as rapid prototyping, post-production assembly, or logistics support.
- Cost Structures: Understand their pricing model to ensure it aligns with your budget without compromising quality.
Future Trends in Plastic Injection Mold Tooling
The field of plastic injection mold tooling is continually evolving. Some emerging trends include:
- 3D Printing Integration: Utilizing 3D printing in the tooling process for faster prototyping and design iterations before committing to traditional mold-making.
- Smart Manufacturing: Implementing IoT technologies for real-time monitoring and predictive maintenance of molding processes.
- Sustainability: A shift towards biodegradable and recycled plastics in response to environmental concerns, prompting innovations in mold designs and materials.
- Industry 4.0: Embracing automation and smart technologies to enhance productivity and reduce time-to-market.
Conclusion
In conclusion, plastic injection mold tooling service plays an indispensable role in the manufacturing landscape. Understanding the process, benefits, and future trends can empower businesses to leverage this technique effectively. Whether in automotive, aerospace, or consumer electronics, mastering injection molding can lead to significant competitive advantages. For comprehensive solutions tailored to your needs, visit Sumiparts today.